Complete
Preform PET mould design process
20L Wine Bottle Preform & Blowing Mould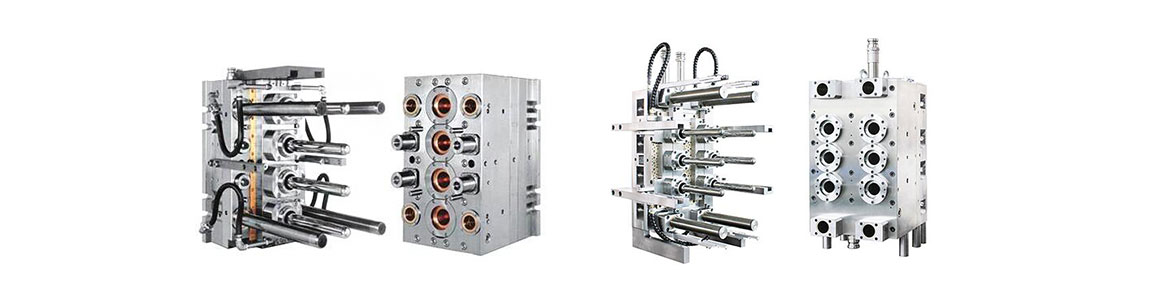
Eternal life pursues the highest mold performance. Produce high quality preforms and use corrosion resistant steel to optimize preform production. Yongsheng mold has a long life. The mold design guarantees quick and easy maintenance. Yongsheng molds are easy to use, and regular maintenance work can be done directly on the machine in the shortest possible time. Mold parts are easy to replace and can produce different preforms on the same mold. Hard mold parts guarantee mold life and minimize maintenance. We can product 2-16 cavity 5 gallon self-lock preform mould, it can blow 20L 30L 40L 50L and more bigger bottle. At present, there are three series of PET preform molds, including double lock pneumatic needle valve tube blank mold. Double lock adjustable eccentric pneumatic needle valve preform mold, ordinary no-gate preform mold. The company uses advanced CAD for mold-assisted design. The shape of the preform is optimized for the final plastic bottle to ensure the final plastic molding quality. The double-lock pneumatic needle valve tube blank mold and the double-lock adjustable eccentric pneumatic needle valve preform mold adopt multi-dimensional cone positioning system to ensure the plastic thickness of the plastic bottle is consistent. At the same time, the unique hot runner system of Yongsheng Mould ensures the same pressure and PET flow ratio of each cavity.
Step 1: Analyze and digest the 2D and 3D drawings of the product, including the following aspects:
1. The geometric shape of the product.
2. The size, tolerance and design basis of the product.
3. The technical requirements of the product (i.e. technical conditions).
4. The name, shrinkage and color of the plastic used in the product.
5. The surface requirements of the product.
Step 2: Determination of the injection type
The determination of injection specifications is mainly based on the size and production batch of plastic products. When choosing an injection machine, designers mainly consider the plasticizing rate, injection volume, clamping force, effective area for installing the mold (internal distance between the tie rods of the injection machine), capacity modulus, ejection form and fixed length. If the customer has provided the model or specification of the injection used, the designer must check its parameters. If the requirements cannot be met, he must discuss with the customer for replacement.
Step 3: Determination of the number of cavities and arrangement of cavities
The determination of the number of mold cavities is mainly based on the projected area of the product, geometric shape (with or without side core pulling), product precision, batch size and economic benefits.
The number of cavities is mainly determined based on the following factors:
1. The production batch of the product (monthly batch or annual batch).
2. Whether the product has side core pulling and its treatment method.
3. Dimensions of the mold and the effective area of the injection molding installation mold (or the inner distance between the tie rods of the injection machine).
4. Product weight and injection volume of injection machine.
5. The projected area and clamping force of the product.
6. Product precision.
7. Product color.
8. Economic benefits (production value of each mold).
The above factors sometimes restrict each other, so when determining the design scheme, coordination must be carried out to ensure that the main conditions are met. After the number of strong characters is determined, the arrangement of the cavities and the layout of the positions of the cavities are carried out. The arrangement of the cavity involves the size of the mold, the design of the gating system, the balance of the gating system, the design of the core-pulling (slider) mechanism, the design of the insert core and the design of the hot runner system. The above problems are related to the selection of parting surface and gate position, so in the specific design process, necessary adjustments should be made to achieve the most perfect design.
Step 4: Determination of the parting surface
The parting surface has been specified in some foreign product drawings, but in many mold designs, it must be determined by the mold personnel. Generally speaking, the parting surface on the plane is easier to handle, and sometimes it encounters a three-dimensional form. Special attention should be paid to the parting surface. The selection of the parting surface should follow the following principles:
1. It does not affect the appearance of the product, especially for products with clear requirements on the appearance, more attention should be paid to the impact of the type on the appearance.
2. It is beneficial to ensure the accuracy of the product.
3. It is beneficial to mold processing, especially the processing of cavity. First return agency.
4. It is beneficial to the design of pouring system, exhaust system and cooling system.
5. It is conducive to the demoulding of the product, ensuring that the product stays on the side of the moving mold when the mold is opened.
6. It is convenient for metal inserts.
When designing the lateral parting mechanism, it should be ensured that it is safe and reliable, and try to avoid interference with the setting mechanism, otherwise a pre-returning mechanism should be installed on the mold.